by Richard W. Wise, G.G.
©2010
In the old days an apprentice goldsmith was required to submit a finished work, sort o final exam and thesis in metal to prove his skills and worthiness to hold the title of master goldsmith. This work was known as a masterpiece.
Per usual at R. W. Wise, a client’s purchase of a particularly beautiful gemstone began the journey. The stone, a fairly large custom cut amethyst measuring 24 x 19mm, a tad large for a ring, practically begged to be made into a brooch. In consultation with our client, it was decided that it would be a combination piece that would be wearable as both a pendant and a brooch.
The client is particularly drawn to designs from The Art Nouveau Period (1890-1910). Le art nouveau, literally the new art, evolved from the Arts & Crafts Movement (1860-1880), really a philosophy as much as a movement that put great emphasis on naturalistic design, hand craftsmanship and the use of honest materials.
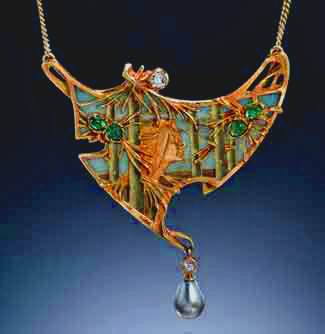
A 18k gold, plique a jour pendant by Art Nouveau master Lucien Gautrait. R. W. Wise Collection. Photo: Jeff Scovil
Art Nouveau jewelers retained the design concept but pulled out the stops when it came to use of materials. Drawing inspiration from ancient Celtic and Gothic designs, jewelry of this period are executed with naturalistic, often fantastical females and floral designs featuring asymmetrical whiplash like filigree. Art Nouveau designs are often quite intricate, made extensive use of enameling as well as exotic gemstones of all colors.
From Concept to Completion:
The Concept:
As with all custom design, the first step is the concept. The client supplied us with pictures of period designs. Master goldsmith Michael Corneau then reinterpreted the design ideas into a pendant/brooch that would frame the gemstone.
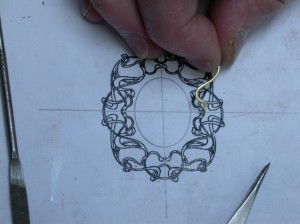
The finished sketch. The empty center is precisely the size of the gemstone. At the upper left the designer holds a narrow piece of shaped 18k gold wire the first section of the piece. Photo: Amy Judd
Execution:
Once the sketch is approved, we move on to execute the design. In this case the construction involved a large number of individually shaped elements.
The following images illustrate the construction process:
The finished Piece: